In the world of property development, cost overruns and last-minute design changes are often accepted as part of the process. But what if they didn’t have to be? According to Alan Tan, our Partner in Victoria, there’s a significant yet underutilised opportunity to take control of project costs long before a single shovel hits the ground, during the design development stage.
“Construction cost is considered the most expensive item in a development project,” Alan stresses. “Often it could equate to half of the total development costs. So, it makes sense to focus on that, but we don’t often see developers invest in updating, optioneering, and managing the construction cost at various design stages.”
At Mitchell Brandtman, we’ve seen time and again that engaging a quantity surveyor throughout the design development stage can make or break the success of a project. There were developers rushing from planning approval to tender, missing out on important stages in the design process. As Alan puts it, “They just go straight to the builder and ask, ‘How much?’. But there’s just not enough information at that point, and that’s where cost surprises come in.”
Costing the Design versus Designing to Cost: A core idea Alan puts as a powerful shift in project thinking is the difference between costing the design and designing to cost. “You’ve got two ways to approach it,” he says. “Costing the design, where you do the design first, then find out the cost. Or designing to cost, where you let the cost guide your decisions as the design evolves. The second approach gives you far more opportunities at lower cost and risk.” Alan shares that at feasibility or business case stage, QSs collaborate with design teams to explore alternatives like repurposing vs. rebuilding, residential vs. commercial, or comparing above-ground and basement parking options. “Without early costing appraisal, how do you know if these options are viable? That’s the kind of strategic input we provide from an early stage.”
Big-Ticket Items and Life Cycle Costing
Alan’s approach is refreshingly pragmatic, which includes material selection and looking at future performance, not just upfront cost.
“We prepare a cost plan that breaks down the individual components so we can identify, say top 10 big-ticket items to review in detail. That’s where the money is. Every 10% – 20% savings on those items could mean hundreds of thousands in real savings.” On the flip side, this doesn’t mean slashing features indiscriminately. “Some expensive finishes and features may only be small quantities, but they add major visual value. So, we appreciate them, especially if the total cost is not significant.”
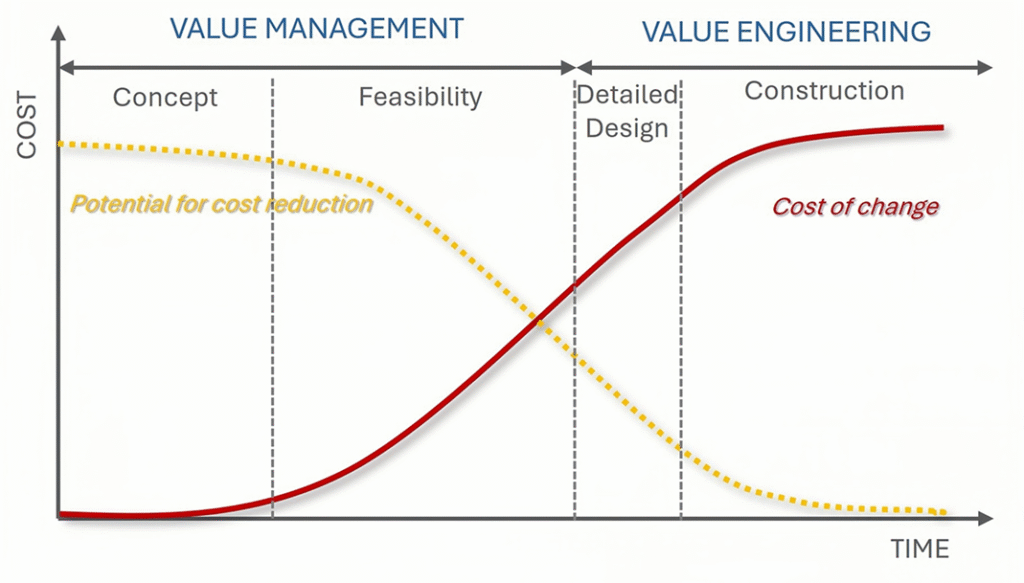
The “Cost of Change Curve”, a concept widely discussed in project management, highlights the importance of early decision-making in project development. Implementing changes during the initial design phases is more cost-effective and less disruptive than making alterations in later stages.
Alan also advocates for life cycle costing and value engineering appraisals. “Sometimes it’s better to spend more now if it means lower maintenance, replacement and fewer disruptions later,” says Alan. “This is especially important in sectors like healthcare, banking and data, where even a day of downtime is catastrophic and costs many times more.” However, he also notes there’s a balance to strike. “…with technology or trend evolving so quickly, it’s often not worth investing heavily in items that will be obsolete in a few years.”
Why Projects Blow the Budget: When asked about the kinds of projects most vulnerable to budget blowouts, Alan indicates that it’s not about project type. “You can have a straightforward project but still blow the budget if you lack cost monitoring, control, and management throughout. Some projects involve Quantity Surveyors at the schematic stage [A]: then stop with no QS involvement during design development stages B and C. Suddenly, QSs are requested to review tender returns. The opportunity to manage cost and value by then is greatly reduced.”
The Value of Expertise Over Automation
So how does a QS offer such tailored advice? It comes down to benchmarking and detailed cost analysis. “We’ve worked on so many types of projects; we have the historical data and benchmarking analysis tools,” says Alan. “We can analyse and compare the costs, functional areas and ratios. That’s how we know where to flag potential issues and opportunities.”
Documentation also plays a major role in cost certainty. Alan adds, “If design documents are incomplete or inconsistent, then you’re going to get variations. BIM and clash detection tools help here, but you still need a human eye to interpret and advise.” In today’s buzz around AI and digital tools, Alan is cautiously optimistic but remains firm on the value of human insight. “It’s a tool, not a substitute for expertise,” he says. “We’re not just measuring and plugging numbers into software. We’re analysing, balancing and managing value for stakeholders throughout the project lifecycle from early stages.”
Final Thoughts
The key message from our interview with Alan Tan: don’t underestimate the value of the design development stage. It’s the best opportunity to add value, minimise waste, and ensure your budget works for the building. In his words, “Quantity Surveyors are not just about cutting costs like in the 1960s or 70s. Today, it’s about guiding design with insight, managing costs early, and making sure every design decision adds long-term value.”
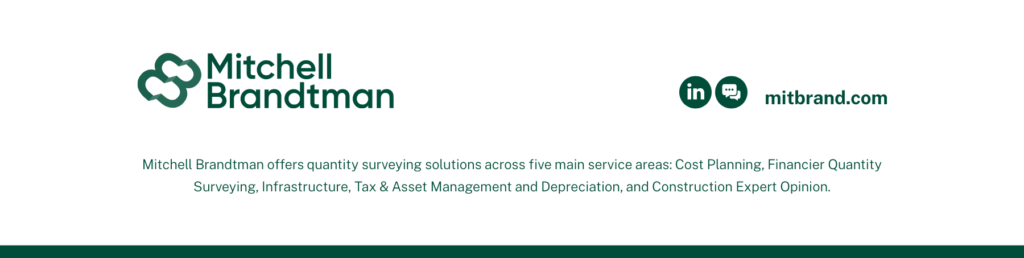